Powering the Future of 5G
Leave a CommentWhen a natural disaster strikes, the impact on the affected communities is devastating. As global temperatures continue to rise, the frequency of severe storms, fires, and other severe weather events are accepted realities rather than catastrophic outliers. These disasters serve as the ultimate stress test for existing infrastructures and often reveal startling weaknesses. In a world increasingly powered by 5G, the need for reliable electrical grid systems is crucial for powering every day and providing backup for unexpected days. Few would argue against the need for more robust backups for telecom networks, but the “how” presents a challenge. Lithium-ion Phosphate (LFP or LiFePO4) batteries are proving to be one of the critical components in answering this challenge.
Responding to Exponential Growth in Power Consumption
The evolution of various communication infrastructures such as 5G, Public Wi-Fi and Edge Networks is causing power consumption to increase exponentially. For instance, the electricity consumed by a base station of a 5G network is about three times that of a 4G base station. The increase in consumption demands a robust backup battery solution to support the network while also being sensitive to cost and green energy considerations.
The telecom industry of the future needs to be Lean, Green, and Keen.
Lean
- Optimize the total cost of ownership
- Reduce deployment costs
- Reduce energy cost of running mobile networks
- Pole mount solutions that are less bulky
Green
- Reduce site visits
- Reduce the energy consumption of running mobile networks
Keen
- Accelerate the deployment of infrastructure
- Increase cycle life
- Reduce charge time
- Increase voltage to overcome voltage drops in the cables
- Wider operating temperature range
- Access premium Real Estate
Considering Lithium vs Lead-Acid
Lithium batteries are smaller and lighter than lead-acid batteries. Furthermore, they demonstrate higher energy density, higher availability, longer service life, more cycle times and reduced TCO. Excell Battery has a range of battery solutions to service the network expansion, for example, the Rack Mount 4.8kW System. Some technical challenges require a higher voltage to handle voltage drops over lines, and Excell’s battery solutions also take this into account.
Advantages of Lithium-Ion Batteries
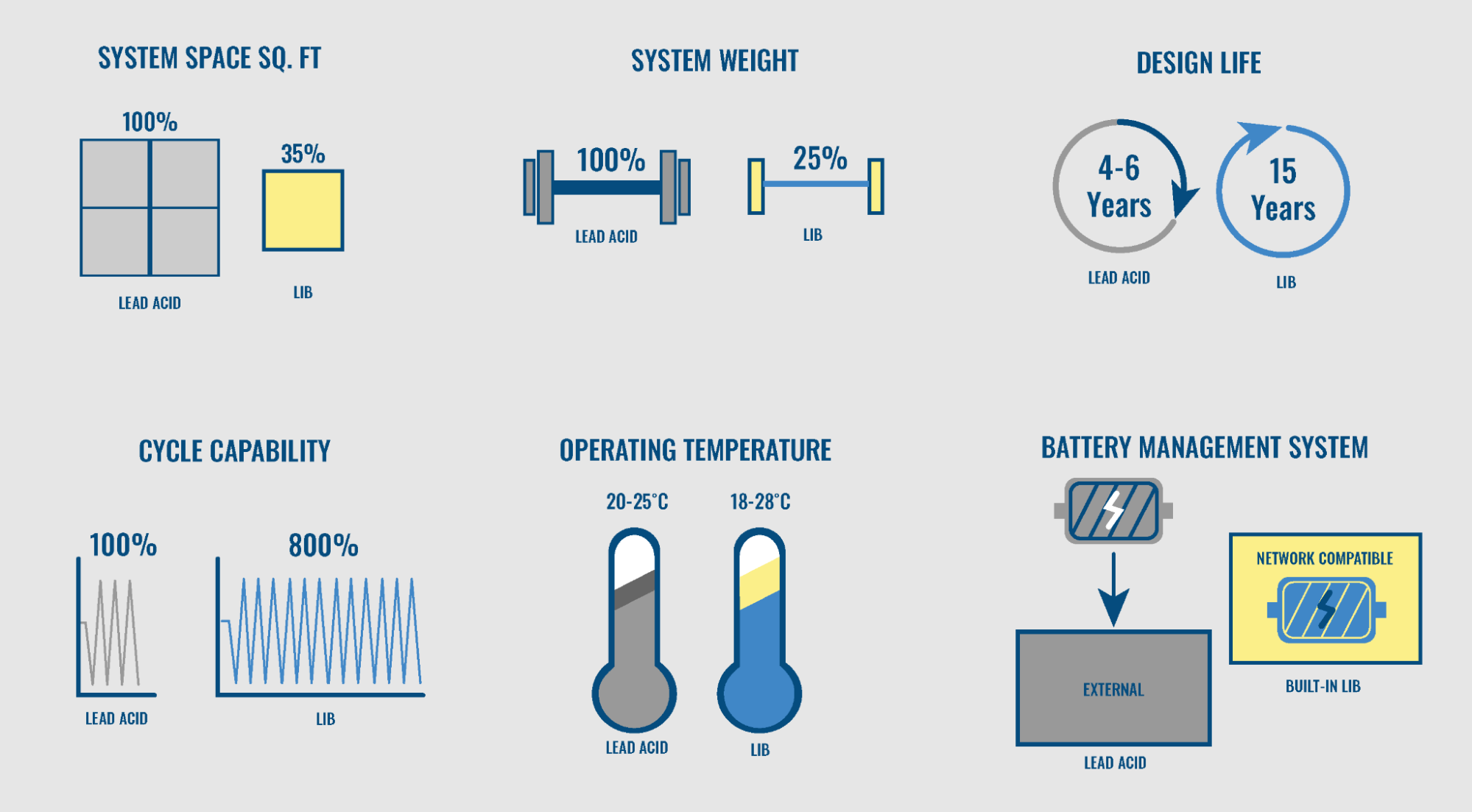
LiFePo4 (or LFP) battery systems have a much lower total cost of ownership than traditional lead-acid (Pb) batteries, leading to enhanced competitiveness and increased profitability. These batteries are increasingly replacing lead-acid batteries in telecom networks as they provide higher energy density.
With the signal ranges in 5G networks running shorter than those in 4G networks, the rollout will require more base stations to provide coverage, particularly in cities, requiring more backup power. LFPs aren’t just smaller and lighter than lead-acid batteries. They also boast higher energy density, higher availability, longer service life and will continue to perform for many more charge/discharge cycles.
High power density generates a 70% smaller footprint than lead-acid batteries. LFP is currently one of the safest cathode materials for lithium batteries, making LiFePo4 batteries the best choice for various scenarios.
LFP modules with Criterion Smart Battery technology integrated into the system to allow for remote monitoring and management. LFPs coupled with smart site management controls improve site resiliency and can cut operating expenses by up to 80%, offering a crucial advantage that will become the industry standard as energy and operating costs continue to rise.
Have more questions? Our design team at Excell Battery is ready to assist with developing your power solution.